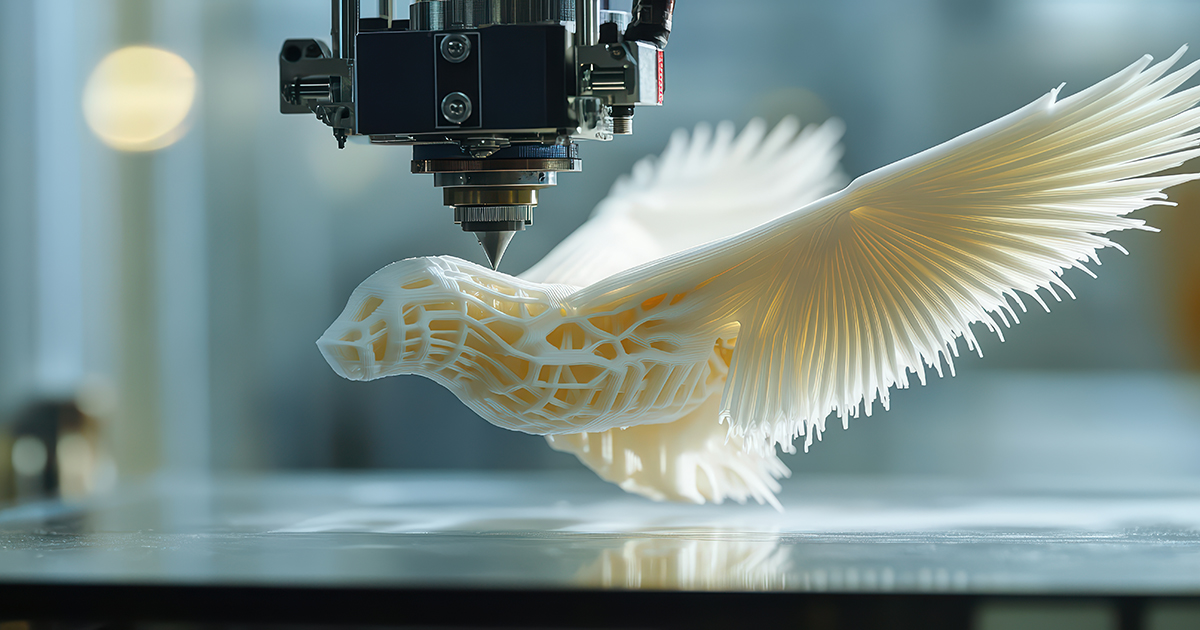
Introduction to CNC Machining and its Purpose
CNC Machining is Revolutionizing The aerospace industry stands at the forefront of innovation, constantly pushing boundaries and reaching new heights. At the heart of this evolution lies CNC machining, a technology that has transformed how aircraft and spacecraft components are designed and manufactured. From rockets to airplanes, CNC (Computer Numerical Control) machining is reshaping our understanding of what’s possible in aviation. This precision-driven approach not only enhances production efficiency but also elevates performance standards across the board. As we explore five key ways CNC machining is revolutionizing aerospace, you’ll see how it’s paving the way for safer, lighter, and more efficient flying machines that could redefine travel as we know it. Buckle up; the journey through aerospace innovation begins here!
How CNC Machining is Used in Aerospace Industry
CNC machining plays a vital role in the aerospace industry. It enables manufacturers to create precision components essential for aircraft and rockets.
The technology allows for intricate designs that are impossible to achieve with traditional methods. Parts like turbine blades, engine casings, and wing structures benefit from CNC’s accuracy.
Specialized materials used in aerospace, such as titanium and carbon fiber composites, can be machined efficiently. This ensures optimal performance while maintaining weight limits critical for flight safety.
Additionally, CNC machines streamline production processes through automation. They reduce human error and speed up manufacturing timelines significantly.
With the ability to produce complex geometries consistently, CNC machining supports innovations in aerodynamics. As a result, it fosters advancements in fuel efficiency and overall aircraft performance on both commercial flights and space missions.
Advantages of CNC Machining in Aerospace
CNC machining offers unparalleled precision, a critical factor in the aerospace sector. When manufacturing components for rockets and airplanes, even the slightest deviation can lead to significant safety risks. CNC technology ensures exact specifications are met consistently.
Efficiency is another major advantage. Automated processes reduce production time without compromising quality. This leads to faster turnaround times for prototypes and finished products alike.
Customization stands out as well. Aerospace projects often require unique solutions tailored to specific needs. CNC allows for intricate designs that traditional methods struggle to achieve.
Cost-effectiveness plays a vital role too. Despite initial setup costs, the long-term savings from reduced waste and improved productivity make it an attractive option for manufacturers in this industry.
CNC machining enhances repeatability. Once programmed, machines can produce identical parts across multiple batches with minimal variation—an essential feature when maintaining high standards of reliability in aerospace applications.
Examples of Innovative Applications in Aerospace
CNC machining has opened up a world of innovative applications in the aerospace sector. One striking example is its role in manufacturing lightweight components for spacecraft. Designers can create intricate geometries that reduce weight while maintaining strength, critical for launching satellites and exploring deep space.
Another fascinating application lies in producing complex engine parts. CNC machines can craft turbine blades with precision, allowing engines to operate more efficiently at higher temperatures.
Beyond traditional aircraft, this technology also plays a vital role in unmanned aerial vehicles (UAVs). The ability to quickly prototype and produce custom parts accelerates development cycles significantly.
Lastly, 3D-printed structures made possible by CNC techniques are becoming common in aerodynamics testing. These lightweight models help engineers refine designs before moving on to full-scale production. Each application showcases how CNC machining continuously transforms aerospace engineering into an era of enhanced capability and efficiency.
Future Possibilities for CNC Machining in Aerospace
The future of CNC machining in aerospace is brimming with exciting possibilities. As technology advances, we can expect even greater precision and efficiency.
Imagine integrating artificial intelligence with CNC systems. This could lead to real-time adjustments during manufacturing processes, enhancing accuracy while reducing waste.
Additive manufacturing paired with CNC machining opens new avenues for design innovation. Complex geometries that were once impossible may soon become standard practice.
Additionally, the growth of lightweight materials will challenge conventional methods. CNC machining can adapt to these changes, ensuring that components remain both strong and lightweight without sacrificing performance.
Collaboration between aerospace companies and tech startups promises groundbreaking developments as well. The combination of diverse expertise could yield solutions previously thought unattainable.
As sustainability becomes increasingly crucial, techniques like recycling metal shavings into new parts may gain traction within the industry. This shift could significantly reduce environmental impact while maximizing resource efficiency.
Potential Challenges and Limitations
While CNC machining presents numerous advantages, it also faces some challenges. One significant hurdle is the initial investment cost. Advanced CNC machines can be expensive, making them less accessible for smaller manufacturers.
Another limitation lies in material constraints. Not all materials are compatible with CNC processes, which can restrict design options for aerospace components. This calls for careful selection during the manufacturing process.
Additionally, skill gaps pose a challenge. Highly skilled operators are essential to maximize the capabilities of CNC technology. There’s often a shortage of trained professionals who understand both aerospace needs and machine operation.
Maintenance requirements cannot be overlooked. Regular upkeep is vital to ensure precision and efficiency over time, which adds another layer of complexity to operations in an industry where safety is paramount.
Conclusion: The Impact of CNC Machining on the Evolution of Aerospace Technology
CNC machining has truly transformed the aerospace landscape. Its precision and efficiency have paved the way for innovations that were once thought impossible. As manufacturers continue to adopt this technology, we can expect even more breakthroughs in design and functionality.
From rockets designed for space exploration to airplanes that enhance passenger safety and comfort, CNC machining plays a pivotal role in every stage of production. The ability to create complex geometries with minimal waste not only boosts performance but also significantly reduces costs.
The continuous evolution of CNC technology promises exciting possibilities ahead. With advancements such as multi-axis machines and automation integration, the future looks bright for aerospace manufacturing.
While challenges remain, including material limitations and initial setup costs, these obstacles are surmountable with ongoing research and development.
As we look towards new horizons in aviation and space travel, it’s clear that CNC machining will be at the forefront of this evolution—shaping the next generation of aerospace technologies in ways we’ve yet to fully imagine. CNC Machining is Revolutionizing